
Sepro ThundeRbot
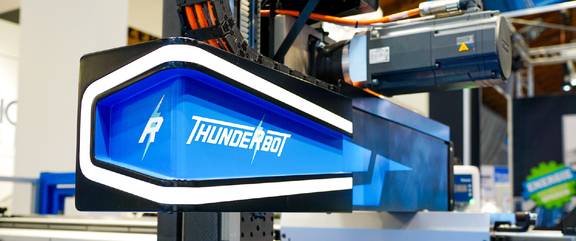
Sepro Design-Innovationen ermöglichen höchste Geschwindigkeiten für „ThundeRbot“
Wie kann man einen Universalroboter so umgestalten, dass er so schnell wie möglich ist?
Das war die Herausforderung für die Ingenieure der Sepro Group, dem weltbekannten französischen Anbieter von Robotern für die Kunststoffverarbeitung. Das Ergebnis dieser Bemühungen – der schnellste Roboter, den Sepro je gebaut hat – ist auf der Fakuma 2023 vom 17. bis 21. Oktober in Friedrichshafen live und mit „Full Speed“ zu erleben. Sepro stellt in Halle A1 am Stand 1203 aus.
Ausgehend von einem Standardroboter des Typs Success 11 8U nahmen die Konstrukteure Änderungen vor, die dazu führten, dass das Handling nur den Bruchteil einer Sekunde benötigt, um ein Kunststoffteil aus einem Spritzgießwerkzeug zu entnehmen. Auf der Fakuma ist der sogenannte „ThundeRbot“ auf einer SumitomoDemag-Spritzgießmaschine zu sehen, die kleine Becher produziert. Die Gesamtzykluszeit beträgt nur 3,07 Sekunden, und die Zeit für das Öffnen des Werkzeugs – die der Roboterarm nutzt und in das Werkzeug einfährt, das Teil entnimmt und wieder herausfährt – liegt bei nur 0,79 Sekunden.
„Wir haben unser Konstruktionsteam herausgefordert. Und es hat jede mögliche Maßnahme zur Erhöhung der Geschwindigkeit umgesetzt“, erklärt Charles de Forges, CEO der Sepro Group. „Was wir hier zeigen, ist eine Konzeptstudie, und so wie Automobilhersteller ‚Concept Cars‘ verwenden, um innovative neue Ideen vorzustellen, ist der ‚ThundeRbot‘ eine Demonstration von Sepro, der verdeutlichen soll, wie innovativ unsere Ingenieure sind. Sie schauen damit, wenn man so will, über den Tellerrand hinaus, um Herausforderungen zu meistern und ein bestimmtes Ziel zu erreichen.“
GEWICHT OPTIMIEREN
Der Schlüssel zum Erreichen schneller Zykluszeiten ist die vertikale Z-Achse des Roboters, die blitzschnell in das Werkzeug einfährt und das Teil entnimmt. Ein neuer Zyklus kann erst beginnen, wenn die Vertikalachse wieder aus dem Werkzeug ausfährt und sich das Werkzeug schließt. Da die zurückgelegten Strecken sehr kurz sind, ist die Endgeschwindigkeit weniger wichtig als die Beschleunigung.
Beim ThundeRbot kann die Z-Achse mit 80 m/s2 (Meter pro Quadrat-Sekunde) beschleunigen. Das ist vergleichbar mit 55m/s2 beim bisher schnellsten Roboter von Sepro (S5-25 Speed) und 30m/s2 beim Standard-Roboter Success. Damit ist die Beschleunigung des ThundeRbot 45 % schneller als die des Speed-Roboters S5-25 und 2,6 Mal schneller als die des Success.
Das zweite Newtonsche Bewegungsgesetz besagt, dass die Beschleunigung eines Objekts umgekehrt proportional zu seiner Masse ist. Eine weniger massive (also leichtere) Z-Achse kann schneller beschleunigen als eine schwerere. Daher konzentrierte sich das Sepro-Team darauf, das Gewicht der vertikalen Tauchachse zu reduzieren und verringerte es schließlich um etwa 6 kg (13,2 lb).
Etwa die Hälfte der Einsparungen wurde dadurch erzielt, dass die Träger der beweglichen Z-Achse aus einem pultrudierten, kohlenstofffaserverstärkten Verbundwerkstoff statt aus Aluminium hergestellt wurden und die linearen Führungsschienen hohl sind. Das bei der Fakuma-Demonstration verwendete End-of-Arm-Tool (EOAT), das am unteren Ende des vertikalen Arms zum Greifen des Spritzteils angebracht ist, wurde 3D-gedruckt. Die Luftleitungen zur Betätigung des Greifers sind in den Greiferkörper integriert, so dass externe Schläuche und Anschlüsse entfallen. Der Rest der Gewichtsreduktion wurde dadurch erreicht, dass die elektropneumatischen Komponenten, die für den Betrieb des Greifers benötigt werden, stattdessen am Arm der Y-Achse (Entformachse) montiert wurden.
Nachdem das Gewicht der Z-Achse reduziert wurde, war es notwendig, die strukturelle Stabilität zu gewährleisten, die zur Bewältigung der höheren Geschwindigkeiten erforderlich ist. Daher besteht der Y-Träger, der den Z-Arm trägt, aus kohlefaserverstärktem Aluminium, um die Steifigkeit zu erhöhen und die Verwindung zu begrenzen. Mit Hilfe der Finite-Elemente-Methode wurde die Konsole unter der Ausquerachse (also die mechanische Schnittstelle zwischen dem Roboter und der festen Aufspannplatte der Spritzgießmaschine) optimiert, um die Steifigkeit zu erhöhen. Schrägverzahnte Zahnstangen (mit weniger Spiel zwischen den Zähnen der Zahnstange und dem Ritzel) verbessern die Übertragung der Antriebskraft und verringern die Geräuschentwicklung. Die Ritzel selbst sind selbstschmierend, so dass keine Fettkartuschen mehr erforderlich sind und weniger Fett abtropfen kann. Diese Innovation wirkt sich nicht auf die Geschwindigkeit aus, sie trägt vielmehr den Kundenwünschen nach einfacher Wartung und allgemeiner Sauberkeit in der Produktion Rechnung.
Auf die Frage, wie diese technischen Innovationen das Design zukünftiger Roboter beeinflussen könnten, antwortete François Bérot, CTO von Sepro, wie folgt: „Aus meiner Sicht könnten die selbstschmierenden Ritzel, der optimierte Konsole und die schrägverzahnte Zahnstange leicht Teil der nächsten Generation von Sepro-Robotern sein. Die Kohlefasertechnologie ist wahrscheinlich zu teuer, um in die Serie einzufließen, aber die Materialien und Prozesse ändern und verbessern sich ständig, so dass sie auf lange Sicht vielleicht realisierbar sind. In der Zwischenzeit arbeiten wir an anderen Möglichkeiten, zum Beispiel an Wabenstrukturen, mit denen sich das Gewicht des Trägers reduzieren ließe, ohne dass Festigkeit und Steifigkeit darunter leiden.“
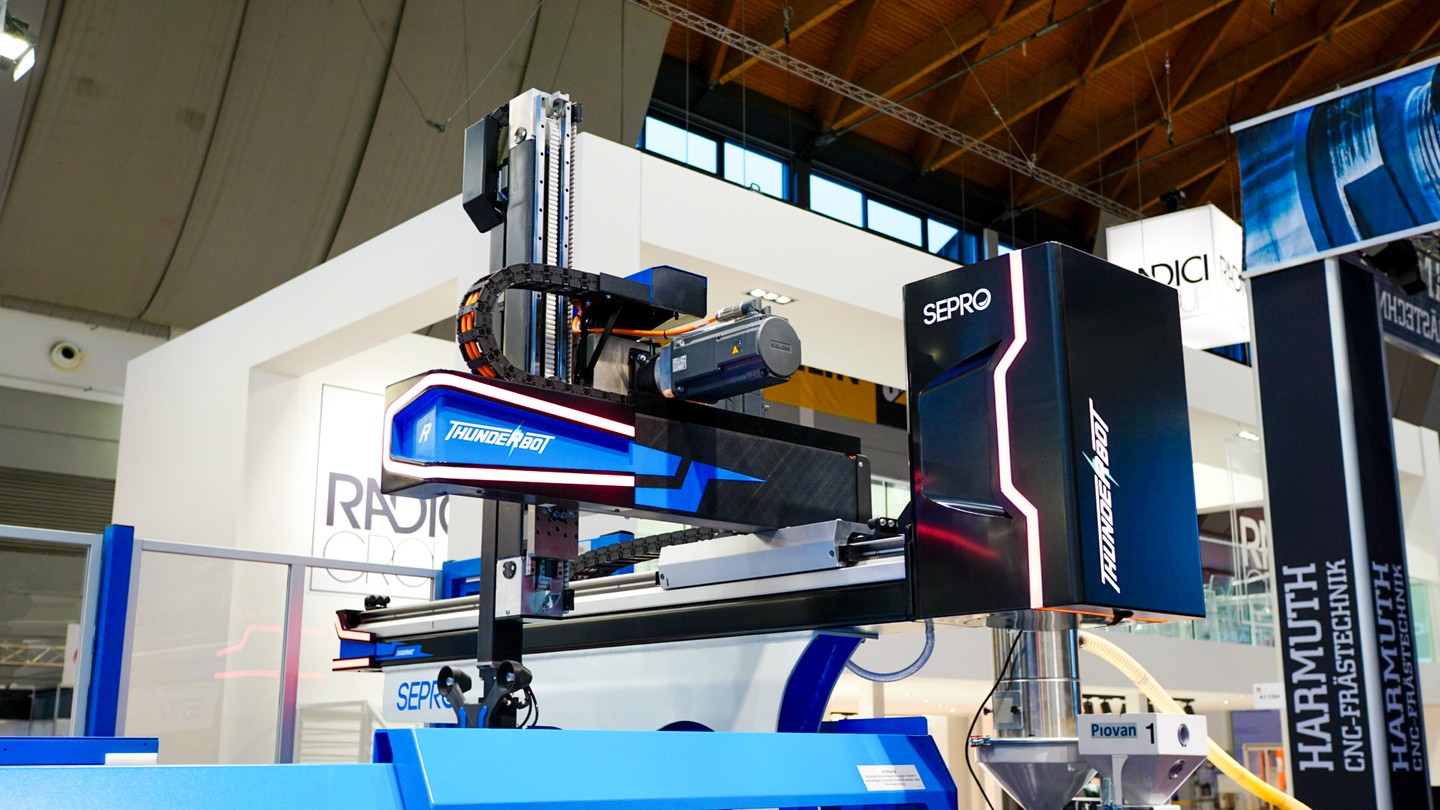
Sepro Newsletter anmelden
Erhalten Sie jeden Monat eine Zusammenfassung unserer Neuigkeiten und Ereignisse